Two principle technologies are the backbone of the coatings industry. They are:
- Liquid paint technology (wet) that was first used by cavemen and has been used industrially for more than 200 years
- Powder coating technology (dry) that has been in use for the last 40 years.
In the simplest terms, powder coating is paint made and supplied in a dry powder form. Powder coating is almost undoubtedly unknown because it contrasts with traditional paints that are liquids applied by brush or spray.

Powder coatings are available in different chemistries and systems to provide decorative and protective finishes for a wide range of end uses.
The use of Powder coatings includes the painting of metal objects. However, newer technologies allow other materials such as MDF, glass, and plastics to be coated.
The use of powder coatings has increased since its inception for several reasons. They provide excellent paint finishes and, because they do not contain solvent, they have a minimal environmental impact.
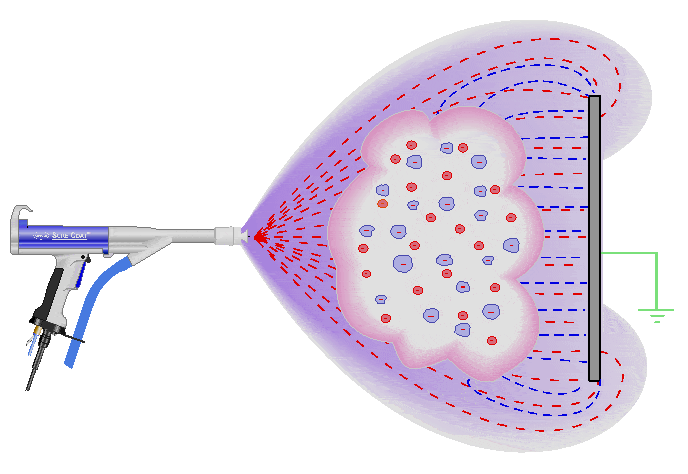
Powder coatings are supplied in boxes or bags, and application is straightforward. The powder is applied to an object using an electrostatic spray gun. Compressed air sucks the dust out its container and pushes it through pipes to the spray gun. At the nozzle of the gun is an electrode, which gives the powder particles a positive charge.
Where can I apply powder coating?
Powder coatings can be applied to almost any metal item that can withstand the typical curing conditions (180-200C for 10-20 minutes) and can fit in an industrial oven. Other substrates, such as MDF, glass, and plastic, can also be coated.
When the appropriate powder formulation is selected, an extensive range of items can be coated. Areas to apply powder paint vary from the body of a car right through to small components inside electric motors. Many objects around us in daily use are powder coated. Washing machines, computers, radiators, metal window frames, alloy car wheels, and furniture are just some examples.
As with any paint, the mixture of ingredients can adapt and adjusted to suit the final end-use. Properties can include resistance to weather for exterior windows, scratch resistance for furniture, and chemical resistance for car components.
Powder coatings have protective properties and also give an excellent decorative appearance. Available in almost any color, there is also an extensive choice of surface finish and gloss levels.
Benefits of powder coating
Powder coatings have numerous benefits as against liquid paints, they:
- contain no solvent
- emit no VOC’s (volatile organic compounds)can produce much thicker coatings without running or sagging
- The powder which does not adhere to the part, called overspray, can be recycled and reused (no wastage)
- production lines produce less hazardous waste than conventional liquid coatings
Application of Powder coating
The method chosen to apply powder coatings is varied depending upon the specific part. Fortunately, powder coating technology offers many choices in the application process. First, we should look at factors to consider in choosing an application method.
Factors to Consider in Coating Methods
- Film thickness requirements
- Line speed
- Part configuration / size / thickness
- Powder coating chemistry
- Product performance characteristics
Then the various application methods available for powder coatings are
- Fluidized Bed
- Electrostatic Fluidized Bed
- Electrostatic (Corona) Spray
- Triboelectric/Tribostatic Spray
- Other various methods including flocking, electrostatic disc, tunnel coaster, flame spray, plasma spray, electromagnetic brush
The two most common ways of applying powder coatings are spraying and dipping, which are summary of the above application methods
Spraying
Powder coatings are ideally suited to high efficiency, fully automated application lines. The powder coating process is equally adaptable to applications requiring flexible manual operations.
The electrostatic spray is a method used to apply thin (25-125 microns) powder films. In some cases, heavier (150-375 microns) films can also be applied. Powder coatings are poured into a powder/air mixture from a feed hopper to the spray gun, which imparts an electrostatic charge on each powder particle by applying a high voltage. The charged powder particles are attracted to the earthed workpiece to be coated and are deposited onto any conductive object within the spray area. However, some of the particles do not accumulate on the workpiece, and it is here that a significant benefit of the powder coating process is identified. The so-called overspray particles recovered can be fed hopper for reuse, which can result in up to 99% of recovery efficiencies.
The coated workpiece is then conveyed to the curing oven. Being solvent-free eliminates the need for solvent flash-off zones, environmental control equipment, or other abatement costs associated with traditional liquid paints. Arising from this are lower fire insurance premiums and a safer work environment.
Another method of charging in some spray gun designs is Tribo Charging. Tribo Charging does not use high voltage, but instead, it uses the principle of high-velocity friction to give the powder particles a static charge.
Dipping
Powder coatings are also applied by dipping into a fluidized bed of powder, made to flow like a liquid by bubbling air through it. A bed of powder is fluidized by blowing air from below through a porous plate. The object to paint is pre-heated to, typically 70-2000C, and immersed in the bed. Depending on the heat sink, the item may require post-heating to affect the curing of the film.
This method is often used for large workpieces such as pipeline, valves, fence posts, etc. or small articles from the electronics industry. These coatings give a thick, tough film with excellent corrosion resistance and good mechanical, electrical insulation, and chemical properties.
For Applications of powder coating in Nigeria contact us.