OILFIELD DRILLING CHEMICALS
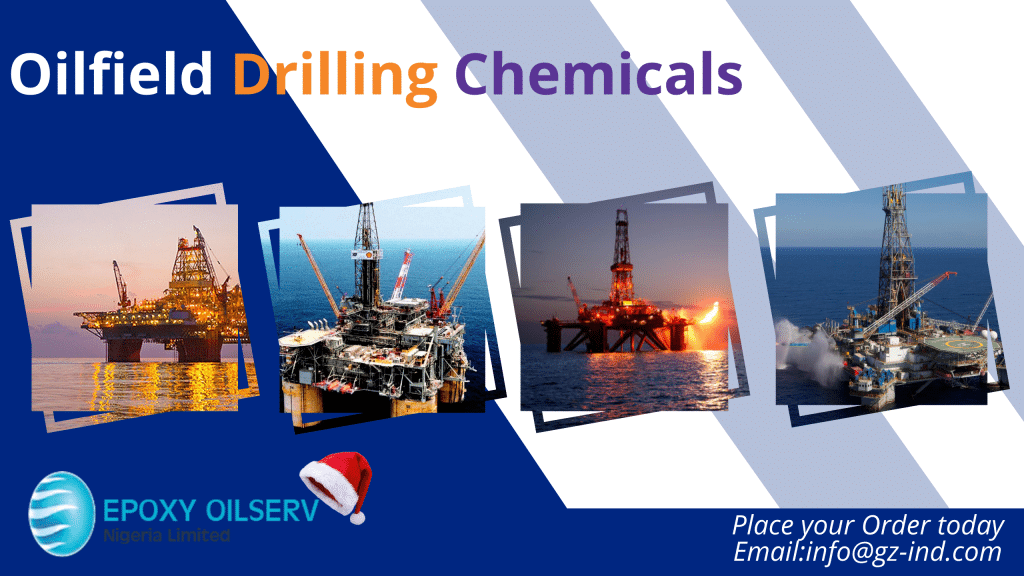
Oilfield drilling is a process of boring hole into to the earth crust for natural gas and oil. To do this, a long bit attached to a “drilling string” is used. The bit varies in diameter from five to 50 inches. After each section is drilled, a steel pipe slightly smaller than the hole diameter is dropped in and often cement is used to fill the gap.This “casing” with cement is used to give some structural integrity to the hole and to isolated high-pressure areas of rock that can explode if allowed to release.
The drilling process can be liken to using a power drill on a piece of wood. The most major difference is that the he hole is filled with “mud” which is often called “drilling mud”. Drilling mud is a mixture of fluids, solids and, chemicals that lubricate the bit, whose function is to cut away from the drill face, provide a hydrostatic head that counters the pressure of gas or oil, and provide a physical and chemical means of stabilizing and protecting the rock formation that is being drilled.
Drilling muds can be used in a very wide variety of rock formations and conditions, their specific composition varies from site to site, and also with different depths in the same well. Since offshore oil and gas exploration began, many different types of substances have been, and are being, used in the formulation and modification of drilling muds which includes emulsifiers, lubricants, wetting agents, corrosion inhibitors, surfactants, detergent, caustic soda, salts, and organic polymers, (https://vaporblash.com/2019/12/11/oilfield-drilling-fluids-chemicals-market-2019-2026-forecast-oil-and-gas-shale-gas/ ) drilling muds also consist of gelling and deflocculating agents (bentonite clays) filtration control agents, pH and ion-control substances, barites, biocides, lubricants, defoaming agents, and trace elements of heavy metals (such as arsenic, barium, chromium, cadmium, lead, and mercury) which can be retained in the oilfield environment .
Functions of some of the chemicals listed;
- Clay and stabilizer listed above, reacts with the wells or boreholes water phase of the drilling fluid to improve its stickiness, induce sloughing and increasing its swelling capacity. The stabilizer is designed in a way that it always adheres to the wall surfaces of boreholes and drill cuttings. With this, encapsulation process can effectively seal surfaces and prevent the reactions between the surfaces and the fluid to prevent undue consequences such as swelling, sticking and sloughing. The aim of this is supposed to boost the stability of the borehole.Eg organophilic clay, bentonite etc.
- Thinners are also referred to as deflocculants. They are thinning agents used to reduce the extent of viscosity or preventing flocculation. Thinners are often incorrectly referred to as dispersants. However, a thinner tend to come in form of low-molecular weight anionic polymer that functions to neutralize the positive charges accumulated on the clay edges. Good examples of thinners include lignosulfates, polyphosphates etc.
- Drilling polymers has high molecular weight fluid with the ability to control the well’s fluid loss and to increase the viscosity. There are over four variants of this chemical which can include polyacrylate, Snergistic polymer, polyglycol, XCD polymer or partly hydrolyzed polyacrylamide.
Oilfield Chemicals are available at our stores nationwide. Please visit our website www.epoxyoil.com
Ruth Ozichu Yakubu
Production Chemist
ruth.yakubu@epoxyoil.com
+234-8060907072